SKORPIONS: behind the scenes
Joanna Berzowska & Marcelo Coelho
SKORPIONS are 5 kinetic electronic garments that use the shape-memory alloy (SMA) Nitinol to move and change on the body in slow, organic motions. The idea of integrating Nitinol into textiles is an obvious way of achieving shape changing, responsive fabrics. However, even though it sounds simple, the process is quite complicated and expensive, as can be seen by the lack of Nitinol-based shape changing garments on the market today.
SKORPIONS integrate electronic fabrics, soft electronic circuits, specially designed circuit boards, Nitinol, mechanical actuators such as magnets, and traditional textile construction techniques such as sculptural folds and drapes of fabric across the body. The cut of the pattern, the seams, and other construction details become an important component of engineering design.
SKORPIONS are not interactive: their programming does not respond to sensor data. They are more like living organisms or moving sculptures that display characteristics such as control, anticipation, and unpredictability.
NITINOL
Nitinol, also known as muscle wire, is a shape memory alloy (SMA) of nickel and titanium that has the ability to indefinitely remember its geometry. The range of applications has been increasing in recent years, especially in medicine, with the development of dental braces that exert a constant pressure on the teeth or stents used to keep arteries open. Due to energy inefficiency, slow response times, and large hysteresis, these materials are not currently appropriate for applications such as robotics or artificial muscles.
During its relaxed (or martensite) state, Nitinol is extremely malleable and resistant; it can be integrated into a soft fabric substrate without causing any disruption in its natural movement and flexibility. On the other hand, once heated to its shape memory (or austenite) state, a Nitinol wire becomes stiff and returns to its original shape with enough force to lift its own weight several times. The shape setting process for the wire happens around 500  C, so it is impossible to shape the Nitinol after integration into the fabric (unless we use materials like Kevlar). This limits design and fabrication possibilities.
To develop the kinetic mechanisms utilized in the Skorpions, it was necessary to explore several custom shaped Nitinol wires and their integration with textile techniques like knitting, sewing, and hand stitching. We did not try the Nitinol in the sewing machine, because it is thicker and more rigid than standard sewing thread.
Nitinol wire that has been previous shape-set can be knit into a wool yarn or stitched onto a surface. The first set of photos show a prototype of knitting Nitinol coils directly into a yarn and the resulting kinetic worms. The second photo shows a prototype of two-colored felt scales that bend to reveal a different color.
Photos by Shermine Sawalha.
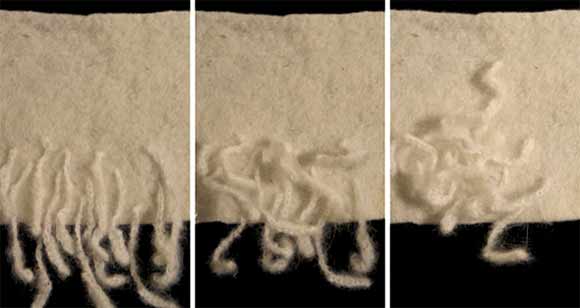
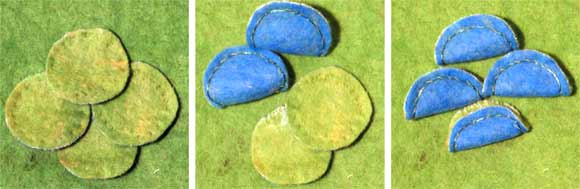
Nitinol wire that has been previous shape-set can be woven into a textile in its martensite state. In the photo, Marcelo connects power to the sample to make it shrink. Photo by Tracey Doyle.
NITINOL FABRICATION
We can control the specific shape-change and the specific temperature at which the change occurs. The material needs to be constrained in the desired shape, heated to 500¬ƒC, and then quenched in water at room temperature. The following photos by Jacques Teisen show the process of shaping the Nitinol wire on a long screw, the furnace where the material is inserted for ’Äúprogramming’Äù the shape, and the final shape memory (or austenite) state.
ELECTRONICS Textiles are traditionally flexible surfaces that can softly envelop the human body. To successfully merge textiles with electronics (which are traditionally hard), we need to develop new methods for making circuits. Our approach at XS Labs involves the use of conductive yarns, inks, and fabrics to allow the construction of soft electronic circuits. The traditional textile materials and construction methods such as sewing, weaving, embroidery, and knitting allow us to merge functionality and aesthetics in our design process. For instance, we connect our custom control electronics to the Nitinol coils with decorative stitching made with conductive thread.
The use of snaps is another technique that allows a durable and seamless connection between the flexible threads and the rigid PCB (printed circuit board). The male snaps are soldered to the PCB, while the female are sewn into the dress and connected to the conductive thread with conductive epoxy. A small inside pocket holds the electronics and insulates them from skin and moisture. This modular assembly allows for the board to be completely removed when necessary, separating soft from hard electronics. photo by Damir Cheremisov
Nitinol is not only used as the scaffold for the desired shape change, but it can also, through resistive heating, produce the heat necessary for actuation. Since the Nitinol wire needs to undergo a temperature change of approximately 40  C to be activated, it requires a considerable amount of power. These requirements are met by two small rechargeable lithium polymer cells that can power the dresses for a couple of hours, depending on the timing and frequency of activation.
Joanna Berzowska & Marcelo Coelho
SKORPIONS are 5 kinetic electronic garments that use the shape-memory alloy (SMA) Nitinol to move and change on the body in slow, organic motions. The idea of integrating Nitinol into textiles is an obvious way of achieving shape changing, responsive fabrics. However, even though it sounds simple, the process is quite complicated and expensive, as can be seen by the lack of Nitinol-based shape changing garments on the market today.
SKORPIONS integrate electronic fabrics, soft electronic circuits, specially designed circuit boards, Nitinol, mechanical actuators such as magnets, and traditional textile construction techniques such as sculptural folds and drapes of fabric across the body. The cut of the pattern, the seams, and other construction details become an important component of engineering design.
SKORPIONS are not interactive: their programming does not respond to sensor data. They are more like living organisms or moving sculptures that display characteristics such as control, anticipation, and unpredictability.
NITINOL
Nitinol, also known as muscle wire, is a shape memory alloy (SMA) of nickel and titanium that has the ability to indefinitely remember its geometry. The range of applications has been increasing in recent years, especially in medicine, with the development of dental braces that exert a constant pressure on the teeth or stents used to keep arteries open. Due to energy inefficiency, slow response times, and large hysteresis, these materials are not currently appropriate for applications such as robotics or artificial muscles.
During its relaxed (or martensite) state, Nitinol is extremely malleable and resistant; it can be integrated into a soft fabric substrate without causing any disruption in its natural movement and flexibility. On the other hand, once heated to its shape memory (or austenite) state, a Nitinol wire becomes stiff and returns to its original shape with enough force to lift its own weight several times. The shape setting process for the wire happens around 500  C, so it is impossible to shape the Nitinol after integration into the fabric (unless we use materials like Kevlar). This limits design and fabrication possibilities.
To develop the kinetic mechanisms utilized in the Skorpions, it was necessary to explore several custom shaped Nitinol wires and their integration with textile techniques like knitting, sewing, and hand stitching. We did not try the Nitinol in the sewing machine, because it is thicker and more rigid than standard sewing thread.
Nitinol wire that has been previous shape-set can be knit into a wool yarn or stitched onto a surface. The first set of photos show a prototype of knitting Nitinol coils directly into a yarn and the resulting kinetic worms. The second photo shows a prototype of two-colored felt scales that bend to reveal a different color.
Photos by Shermine Sawalha.
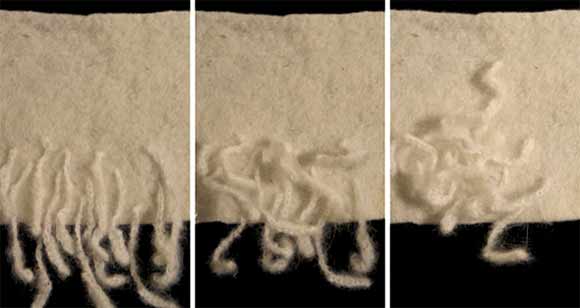
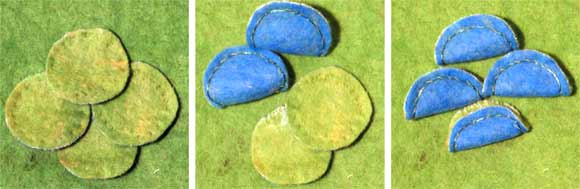
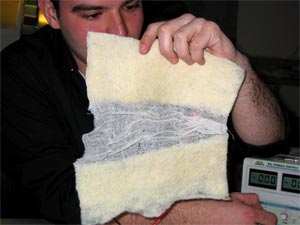
NITINOL FABRICATION
We can control the specific shape-change and the specific temperature at which the change occurs. The material needs to be constrained in the desired shape, heated to 500¬ƒC, and then quenched in water at room temperature. The following photos by Jacques Teisen show the process of shaping the Nitinol wire on a long screw, the furnace where the material is inserted for ’Äúprogramming’Äù the shape, and the final shape memory (or austenite) state.
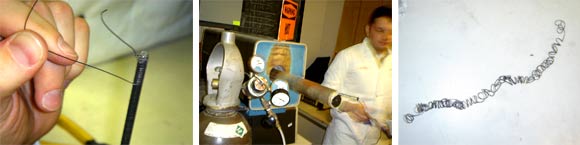
ELECTRONICS Textiles are traditionally flexible surfaces that can softly envelop the human body. To successfully merge textiles with electronics (which are traditionally hard), we need to develop new methods for making circuits. Our approach at XS Labs involves the use of conductive yarns, inks, and fabrics to allow the construction of soft electronic circuits. The traditional textile materials and construction methods such as sewing, weaving, embroidery, and knitting allow us to merge functionality and aesthetics in our design process. For instance, we connect our custom control electronics to the Nitinol coils with decorative stitching made with conductive thread.
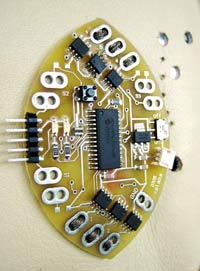
Nitinol is not only used as the scaffold for the desired shape change, but it can also, through resistive heating, produce the heat necessary for actuation. Since the Nitinol wire needs to undergo a temperature change of approximately 40  C to be activated, it requires a considerable amount of power. These requirements are met by two small rechargeable lithium polymer cells that can power the dresses for a couple of hours, depending on the timing and frequency of activation.